When it comes to the production of industrial-grade nylon filament, the manufacturing process is a crucial aspect that directly impacts the quality and performance of the final product. In this article, we will delve into the intricate details of how nylon filament is manufactured for industrial use, shedding light on the various stages and techniques involved in the process.
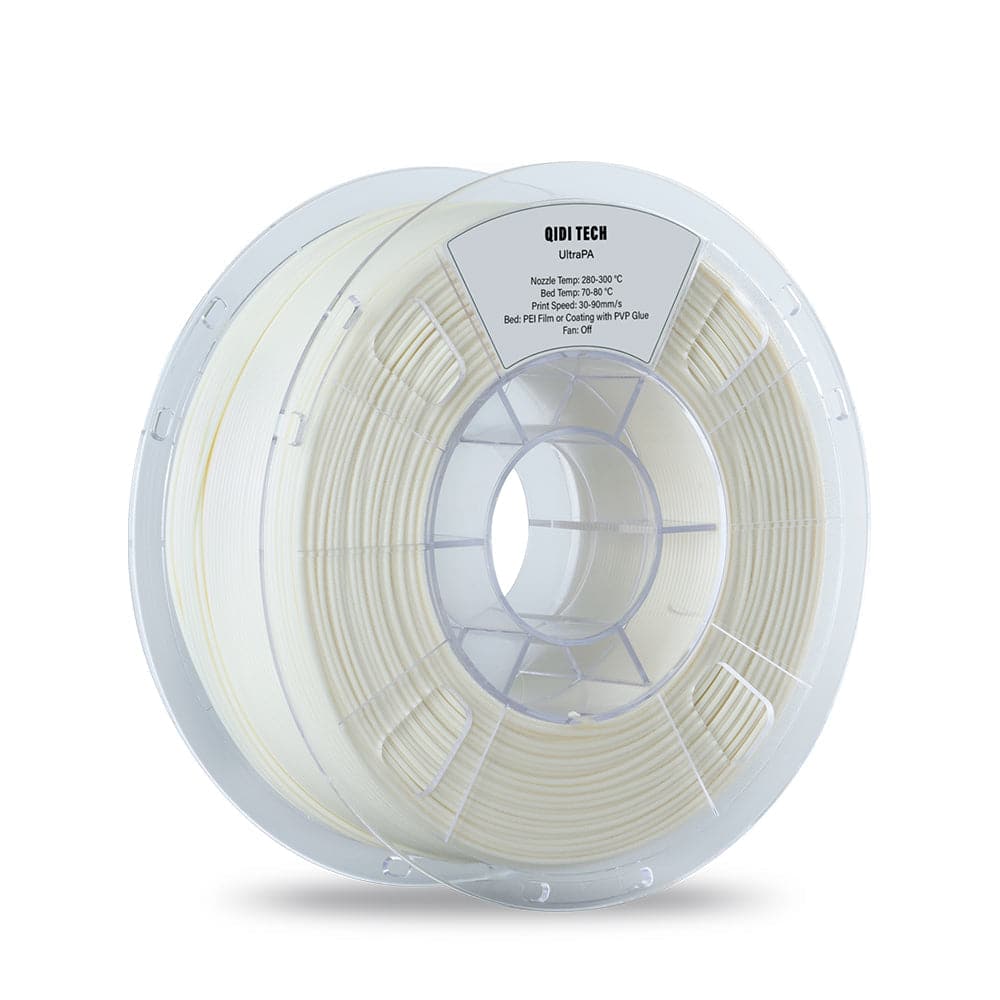
The Chemistry Behind Nylon Filament
Before delving into the manufacturing process, it's essential to understand the chemistry behind nylon filament. Nylon, a synthetic polymer, is created through a chemical process known as polycondensation. This process involves the reaction of two monomers - adipoyl chloride and hexamethylenediamine - to form a long-chain polymer, which is then extruded to create the filament. The molecular structure of nylon gives it exceptional strength, durability, and resistance to abrasion, making it an ideal material for industrial applications.
Extrusion Process
The extrusion process is a fundamental step in the manufacturing of nylon filament. The process begins with the melting of nylon chips, which are then fed into an extruder. Inside the extruder, the molten nylon is forced through a spinneret, a metal plate with tiny holes, to create continuous filaments of the desired diameter. The filaments are then cooled and solidified to maintain their shape and structure. This extrusion process is crucial in determining the diameter, uniformity, and tensile strength of the nylon filament, making it a critical stage in the manufacturing process.
Draw Texturizing
After the extrusion process, the nylon filament undergoes draw texturizing, a mechanical process that imparts texture and bulk to the filaments. During draw texturizing, the filaments are stretched and bulked to enhance their elasticity, softness, and bulkiness, making them suitable for various industrial applications such as textile manufacturing, automotive components, and industrial machinery. This stage of the manufacturing process plays a significant role in enhancing the physical properties of the nylon filament, making it versatile and adaptable for a wide range of industrial uses.
Heat Setting
Heat setting is a critical stage in the manufacturing process of nylon filament, where the filaments are subjected to controlled heat to stabilize their molecular structure and dimensions. This process helps to reduce the residual stresses in the filaments, improve their dimensional stability, and enhance their resistance to heat and moisture. Heat setting also imparts a degree of memory to the filaments, allowing them to retain their shape and structure even under extreme conditions. This stage of the manufacturing process is essential in ensuring the quality, performance, and reliability of the nylon filament for industrial use.
In conclusion, the manufacturing process of nylon filament for industrial use is a complex and intricate process that involves various stages and techniques to produce high-quality, durable, and versatile filaments. From the chemistry of nylon to the extrusion, draw texturizing, and heat setting processes, each stage plays a crucial role in shaping the properties and characteristics of the nylon filament. By gaining a deeper understanding of the manufacturing process, manufacturers and industrial users can make informed decisions and harness the full potential of nylon filament for a wide range of industrial applications.